Injection molding is a widely used manufacturing process for creating plastic parts in various industries. An injection molding machine is a critical piece of equipment in this process. In this article, we will discuss how an injection molding machine functions in detail.
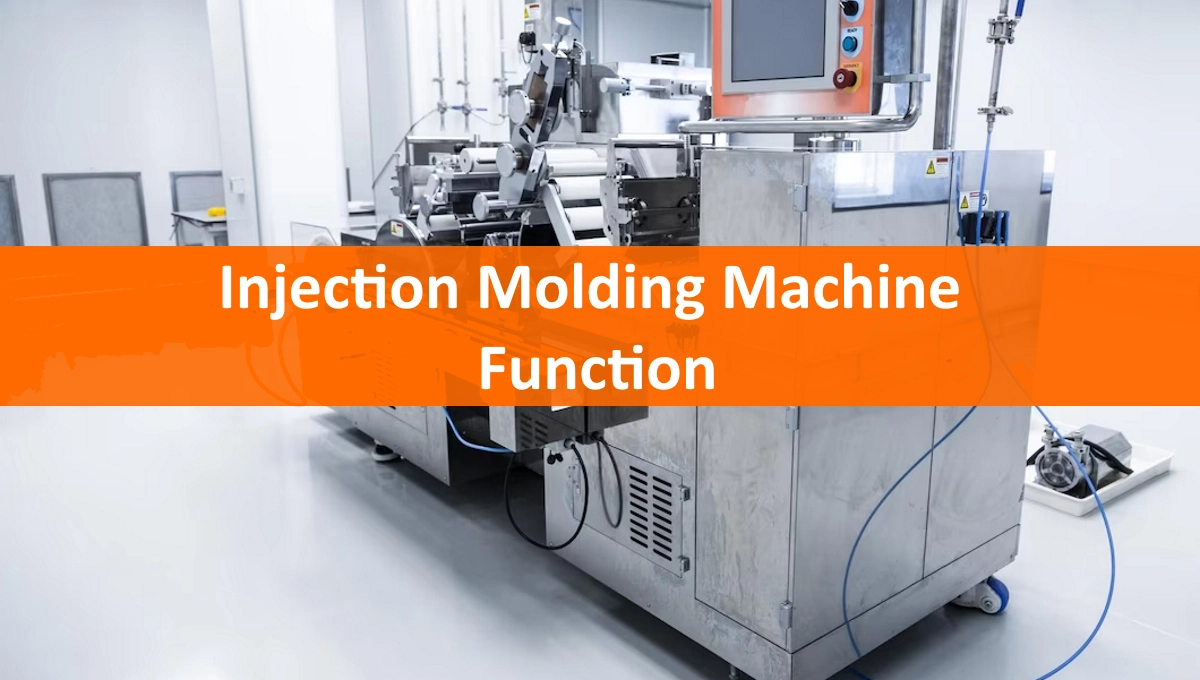
Table of Contents
Introduction
Injection molding is a process used for manufacturing plastic parts by injecting molten plastic material into a mold. Injection molding machines are used to carry out this process. The machine comprises several components that work together to mold the plastic material into the desired shape.
In this article, we will provide an in-depth analysis of how injection molding-machines function.
The Basics of Injection Molding
Before delving into the working of an injection molding machine, let’s first discuss the basics of injection molding.
Injection molding involves feeding solid plastic pellets into a heated barrel. The pellets are then melted into a liquid state by heating the barrel. Once the material has melted, a plunger forces the liquid plastic into a mold cavity. The molten plastic then cools and solidifies to form the final product.
The Components of an Injection Molding Machine
An injection molding machine comprises several components that work together to create plastic parts. The main components of an injection molding machine include the injection unit, clamping unit, and control system.
Injection Unit
The injection unit is responsible for melting and injecting the plastic material into the mold. The unit comprises a hopper, barrel, and screw. The hopper stores the plastic pellets, which are then fed into the barrel. The barrel has a heating element that melts the plastic pellets, and the screw forces the molten plastic into the mold.
Clamping Unit
The clamping unit holds the mold in place during the injection molding process. The unit comprises two plates, one fixed, and one movable. The mold is mounted on the movable plate, which is then clamped onto the fixed plate. The clamping unit ensures that the mold is held securely in place to prevent any deformation during injection.
Control System
The control system is responsible for controlling the entire injection molding process. It comprises several components, including the hydraulic system, electrical system, and computer interface. The control system regulates the temperature, pressure, and timing of the injection molding process.
The Injection Molding Process
The injection molding process consists of four main stages: clamping, injection, cooling, and ejection. Let’s take a closer look at each stage.
Step 1: Clamping
The clamping unit closes the mold, and the mold is held in place with high pressure. This ensures that the mold is not deformed during injection.
Step 2: Injection
The plastic pellets are fed into the barrel, where they are melted by the heating element. The screw forces the molten plastic into the mold cavity, where it takes the shape of the mold.
Step 3: Cooling
After the plastic has been injected into the mold, it begins to cool and solidify. The cooling time depends on the thickness and complexity of the part being molded. Once the plastic has solidified, the mold is opened, and the part is removed.
Step 4: Ejection
In this stage, the part is ejected from the mold. The ejection system uses pins, plates, or air to remove the part from the mold without damaging it.
Types of Injection Molding Machines
There are three main types of injection molding-machines: hydraulic, electric, and hybrid. Let’s take a closer look at each type.
Hydraulic Injection Molding Machine

Hydraulic injection molding-machines are the most common type of machine used for injection molding. These machines use hydraulic cylinders to apply clamping force and injection pressure. They are best suited for large parts and high-volume production runs.
Electric Injection Molding Machine
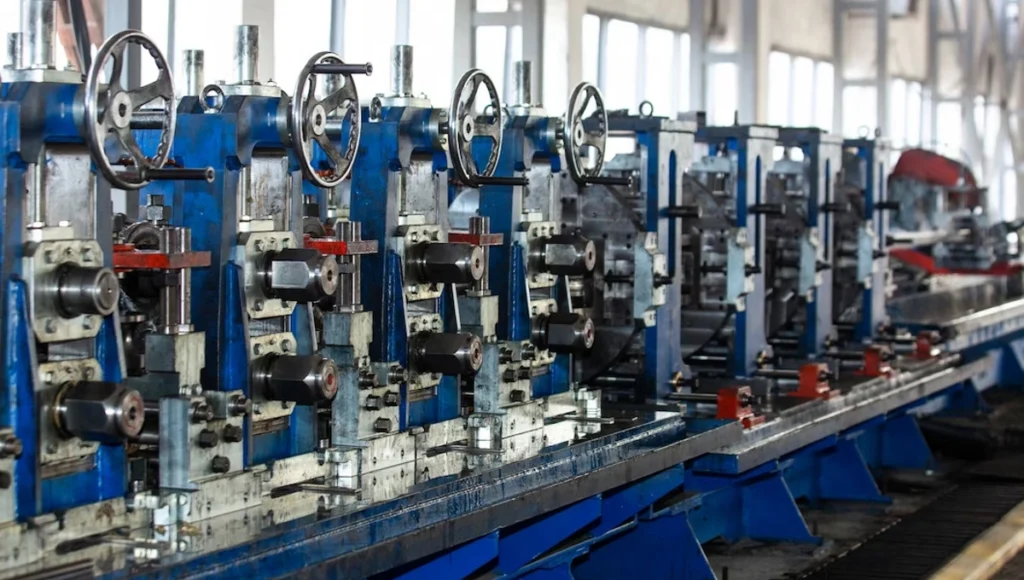
Electric injection molding-machines use electric motors to power the machine. These machines are more energy-efficient than hydraulic machines and are best suited for small to medium-sized parts.
Hybrid Injection Molding Machine
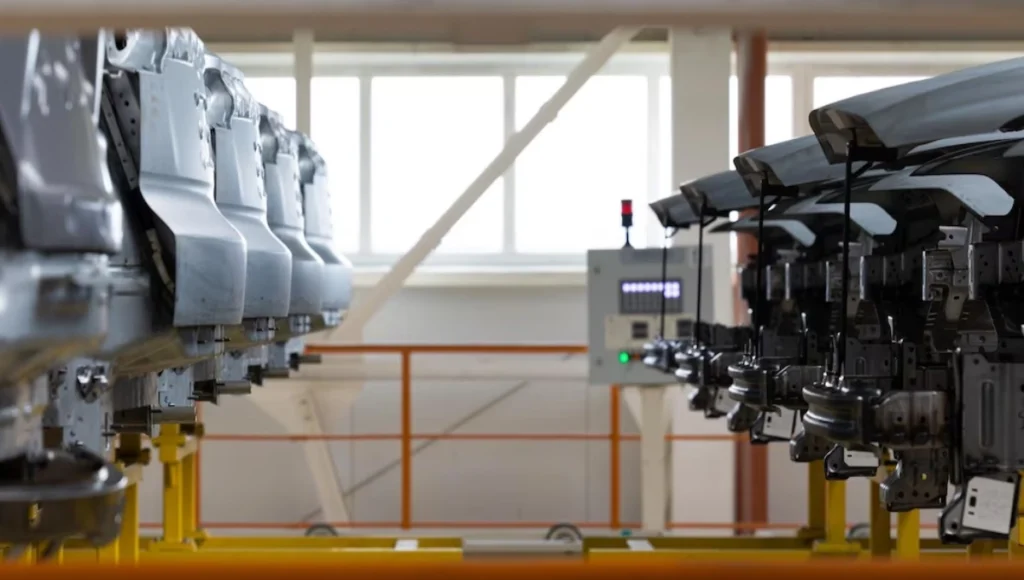
Hybrid injection molding-machines combine the best features of hydraulic and electric machines. They use hydraulic clamping and electric injection to provide high precision and energy efficiency.
Advantages of Injection Molding Machines
Injection molding-machines offer several advantages, including:
- High production rate: Injection molding-machines can produce large quantities of parts in a short amount of time.
- High accuracy and precision: Injection molding-machines can create parts with high accuracy and precision, ensuring that each part is consistent.
- Flexibility: Injection molding-machines can produce parts of various sizes and shapes, making them suitable for a wide range of applications.
- Low labor cost: Injection molding-machines require minimal human intervention, reducing labor costs.
Limitations of Injection Molding Machines
While injection molding-machines offer several advantages, there are also some limitations to consider, including:
- High initial cost: Injection molding-machines are expensive to purchase and maintain.
- Limited material selection: Injection molding is only suitable for certain types of materials, such as thermoplastics.
- High tooling costs: Injection molding requires molds that are expensive to design and produce.
- Limited design flexibility: Injection molding is best suited for simple to moderately complex parts.
Maintenance and Troubleshooting of Injection Molding Machines
Like any other machine, injection molding-machines require regular maintenance to ensure that they continue to function properly. Common maintenance tasks include cleaning, lubricating, and inspecting the machine. Troubleshooting may also be necessary to resolve any issues that arise during operation.
Safety Considerations
Injection molding-machines can be hazardous if proper safety measures are not taken. Operators should receive proper training on the safe use of the machine and should follow all safety protocols. Safety measures include using proper protective equipment, such as gloves and safety glasses, and following proper lockout/tagout procedures.
Future of Injection Molding Machines
Injection molding-machines are expected to continue to play a crucial role in the manufacturing industry. Advancements in technology, such as the use of artificial intelligence and machine learning, are expected to further improve the efficiency and accuracy of injection molding-machines.
Conclusion
Injection molding-machines are critical equipment in the manufacturing industry. They enable the production of plastic parts with high accuracy and precision. Understanding how these machines function is essential for anyone involved in the manufacturing process.
Also you can read about
- How to Deploy DAG (16) easily in Exchange Server
- How quickly to Deploy director Server in 1 Skype for Business Server Environment
- Swiftly Set Up Autodiscover Internally and Externally on 1 Exchange Server
- How to Install Skype for Business Server 2015 Standard Edition Step by Step
- Troubleshooting Spotify DJ Not Showing Up
FAQs
What is injection molding?
Injection molding is a process used for manufacturing plastic parts by injecting molten plastic material into a mold.
What are the main components of an injection molding machine?
The main components of an injection molding machine include the injection unit, clamping unit, and control system.
What types of materials can be used in injection molding?
Injection molding is best suited for thermoplastics, which can be melted and solidified repeatedly without degradation.
What is the difference between hydraulic, electric, and hybrid injection molding machines?
Hydraulic machines use hydraulic cylinders for clamping and injection, electric machines use electric motors, and hybrid machines combine both hydraulic and electric systems.
How can I ensure the safety of operators using injection molding machines?
Proper training, the use of protective equipment, and following lockout/tagout procedures are essential to ensuring operator safety.
Don’t forget to support us by following us on Google News or Returning to the home page TopicsTalk
Join Telegram and WhatsApp for More updates
Follow us on social media